Learning (investigating) things that go wrong?
16 June 2015Companies safety policies and thresh hold values are quite explicit when it comes to well's, equipment, down hole, process or productivity failure/loss values.
Note: This is particularly important as 95% of accidents/incidents we know are non-injury related?
Thus majority of failure events are well's equipment, systems, process, productivity/loss driven!!!
In high value wells this may only equate to a 4-6hr downtime, loss or waste related event, or less if constituted as a reportable and investigative event as per each companies QHSE matrix?
Q1) Where are the investigative reports for these events and what are the findings, the learning's?
Q2) How are small to major accidents/incident/ failure events (non-injury related), actually being reported and investigated on your well's drilling projects? If they are, what specific methods are being employed?
Q3) Why is there both individual and organisational failure to report and investigate such events?, particularly when company policy and QHSE statement is quite explicit and clear?
e.g. From my experiences when 'things go wrong' on the drill floor or down-hole. What normally results is that the driller or the DSV commonly ends up with the proverbial warning letter or the slapped wrists. note: Rarely was a formal investigative method employed, or one that we were trained in to find out why things evidently went wrong. For myself, I was never formally trained in how to investigate 'things that go wrong', though I realised that this was a necessary supervisory/leadership soft skill requirement?
Looking back, on all failed events that I had experienced. If these were properly investigated, e.g. the stakeholders involved identified, then based on the (physical, paper, human factor) evidences streams that existed, all stakeholders then asked to explain their contribution and part to play in such events. Surely a true, honest and open reflective picture would emerge and we would get to all the physical, human and latent causes of what, when, how things went wrong, and why people did what they did or had to do for each failed, loss or wasted time event. Thereby learning from all things that went wrong where several (not one) stakeholder is generally involved and that things that went wrong are rarely as they first appear!
All based from the evidence!
Finally what does a company state about it's attitude to safety, when we know, that the majority of small and big events 'all things that go wrong', generally fail to be properly investigated or that their leadership personnel is not trained in how to do so, in such matters?
Comments, viewpoints, experiences, methods being used? appreciated.
6 Answer(s)
PLEASE LOGIN OR SIGN UP TO JOIN THE DISCUSSION
Support Spread
We need the support of our members to keep our forum online. If you find the information on spread useful please consider a donation

Posted by
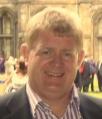
Peter Aird
Drilling Specialist/Well Engineer/Training Consultant
Discussions: 115
Replies: 449
Related Discussions
Multiple drilling then casing/cementing?
17 1/2" riserless drilling
Automated rigs - pros and cons
Semi-Sub Operational Effectiveness
How this site is paid for : excellent performance support from rp-squared
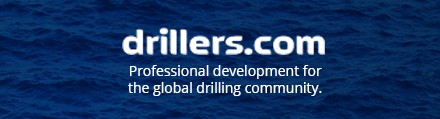
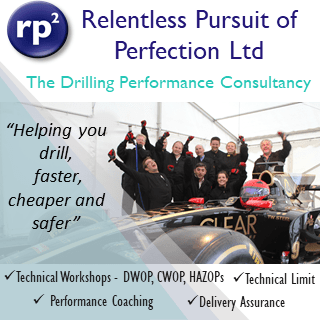