Material selection philosophy for casing
11 January 2010 I'd like to get the forums views on the philosophy for the selection of casing materials in the case of an onshore HPHT project with a reservoir fluid that is moderately sour.In a conventional well that is completed with a packer and tubing string, little or none of the production casing is ever exposed to reservoir fluids. Only in the event of a failure of a primary barrier (hanger, tubing packer etc) is the production casing exposed to such fluids. As such, what are the philosophical or policy approaches used by other operators to guide selection of a suitable casing material?
Regards,
Bruce Richardson
4 Answer(s)
PLEASE LOGIN OR SIGN UP TO JOIN THE DISCUSSION
Support Spread
We need the support of our members to keep our forum online. If you find the information on spread useful please consider a donation

Posted by
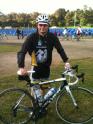
Bruce Richardson
Drilling Specialist
Discussions: 5
Replies: 7
Related Discussions
vam thread
Buoyancy Assisted Casing Equipment
10 3/4" Casing Coupling Clearance
Keeping People off Casing
External coating of surface casing
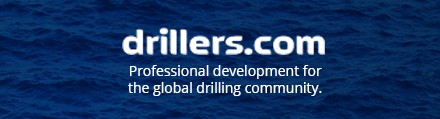
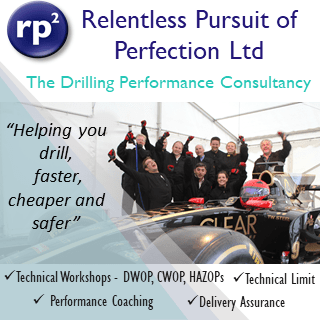