Reversing out excess cement after liner cementation
24 December 2012 Hi folks(As Santa loads up his sleigh with those gifts, I thought I'd ask a question).
At a recent DWOP, we discussed the possibility of reverse-circulating out excess cement after a liner job. The liner is equipped with a liner top packer which will be set as soon as the cement job is finished.
The advantages of doing it this way, compared to normal circulation route, being that :
- it keeps a film of cement from the walls of the casing
- it keeps cement away from the BOP
- it is quicker
- fluid interfaces with cement contamination are less and in many places that helps due to not being able to discharge this interface due to environmental considerations.
The primary disadvantages (that we could think of) are :
- if the packer has not set, then there's the potential to squeeze away the contents of the liner lap, and, depending where losses have occurred, the potential to cause issues with well integrity and/or zonal isolation .. so we would conduct the test in stages
- potential to induce flash-setting of the cement (or so it is claimed), cementing in the tools
- Cement in BOP
- Cement flash-setting
Dave
Dave and the SPREAD team
8 Answer(s)
PLEASE LOGIN OR SIGN UP TO JOIN THE DISCUSSION
Support Spread
We need the support of our members to keep our forum online. If you find the information on spread useful please consider a donation

Posted by
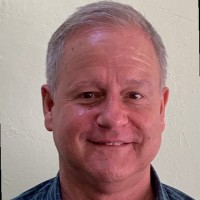
Dave Taylor - SPREAD Moderator
Managing Director (rp-squared.com)
Relentless Pursuit Of Perfection Ltd.
Discussions: 230
Replies: 346
Related Discussions
vam thread
Buoyancy Assisted Casing Equipment
10 3/4" Casing Coupling Clearance
Keeping People off Casing
External coating of surface casing
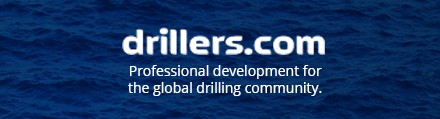
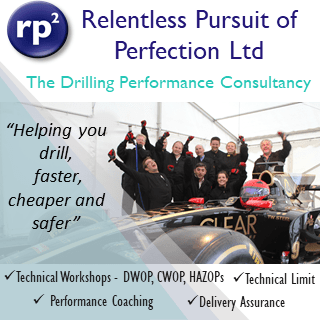