Field Testing Casing above 80% of Burst
I'm currently facing well design issues related to casing pressure test.According to planned architecture, Pore & Frac pressure in Hands, and design file, the Maximum expected Wellhead pressure of my casing will correspond to 91 % of casing burst.
Triaxial design analysis on a well full of gas scenario is showing good results.
However, the associated pressure test required would have to be as high as 91% of Yield.
This test (if performed) would have to be performed having a certain number of mitigations measures in place (light fluid inside casing / test packer to test only required area)
Pure desk engineering considerations are showing achievable results.
However, this is going against common "oilfield" standards calling not to go above 80% of Burst (and I must say against my common sense considering the risks doing this operation in case of failure).
Recognised engineering and design companies are also always remaining that Pressure test should not be a dimensionning load case in any architecture.
My past experience in HPHT has also led me not to test to MEWHP at least for drilling (DST case is not what we are talking about here) in almost all cases...
The maximum documented value found in some Operators standard was 85% of Burst.
My question is the following: Has anybody within this community already experienced and performed hard cement pressure test on the rig at values above 80% (or 85%) of casing Burst for an intermediate casing.
If yes, what was the feedback and what would be your recommendations.
If no, I would also be interested in having your arguments.
If you believe I am a fool trying to conduct such a test, say it :-)
Thank you for your view on this one
David
3 Answer(s)
PLEASE LOGIN OR SIGN UP TO JOIN THE DISCUSSION
Support Spread
We need the support of our members to keep our forum online. If you find the information on spread useful please consider a donation

Posted by
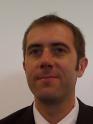
David Vavasseur
Director of Operations
Discussions: 1
Replies: 24
Related Discussions
vam thread
Buoyancy Assisted Casing Equipment
10 3/4" Casing Coupling Clearance
Keeping People off Casing
External coating of surface casing
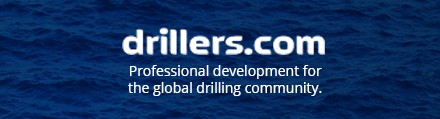
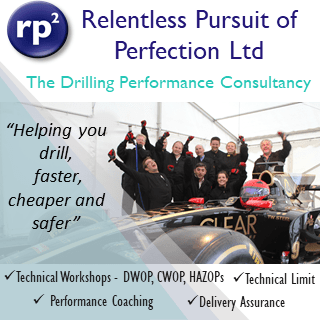