Stump testing BOPs on Jackups
01 February 2014The BOP storage stump on the side of the cantilever beam on an older cantilever jackup does not easily allow for offline stump testing of the BOP stack. Vertical access to the top of the stack is limited and does not allow for a test mandrel to screw into the test stump. Currently, short test mandrels with shoulders that locate beneath the rams are utilized for all sizes except for 9â…" casing rams. Comments on the following issues would be appreciated.
a) Do most jackups routinely stump test prior to N/U on wellhead? Newer generation vs older generation rigs?
b) Common practices for stump testing on cantilever jackups.
c) Use of test mandrels with shoulders which locate beneath the ram to prevent pumping out (as opposed to test mandrels which screw into the test stump). Can they damage the rams? Can they be used on annular preventers?
d) Any incidents with stump testing: launched test joints, damage to BOPs, injuries, etc.
e) Should stump test date start the interval until the next test or should it start when the stump tested BOPs are installed.
f) Do contracts usually require the drilling contractor to stump test BOP prior to installation?
g)Other comments
7 Answer(s)
PLEASE LOGIN OR SIGN UP TO JOIN THE DISCUSSION
Support Spread
We need the support of our members to keep our forum online. If you find the information on spread useful please consider a donation

Posted by

Thomas Emmons
Trainer
Discussions: 3
Replies: 8
Related Discussions
Dynamic transmission fluid effects?
BOP pressure test times
Offline testing of safety valves
Casing rams
Well control after drilling with casing
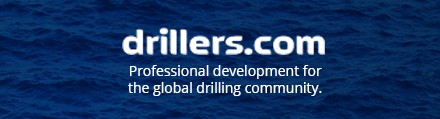
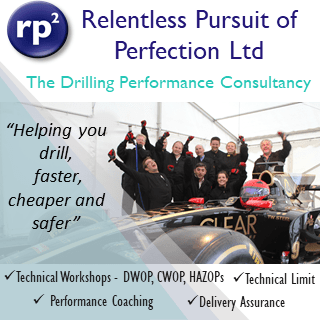