BOP Test Pressure Policy
10 June 2017We are seeking to optimize BOP test times by simultaneously testing the choke manifold at surface and the BOP downhole within the same test. An issue that we face is that for some tests, the Maximum Anticipated Pressure at surface plus the hydrostatic of the fluid in the choke lines exceeds 15,000 psi INTERNAL pressure downhole (rated working pressure of the BOP). While the hydrostatic pressure of seawater at the seabed reduces the NET pressure on the BOP to well below 15,000 psi, some have expressed concern about exceeding the INTERNAL working pressure on the BOP (i.e. could there be chambers within the BOP that are exposed to internal pressure that do not gain the benefit of the hydrostatic back up?).
I was wondering how does other operators approach this issue – do you or would you limit pressures to maximum rated INTERNAL pressure on the BOP or are would you allow your pressure limits to be based upon the NET loading of the BOP (internal – external pressure)?
2 Answer(s)
PLEASE LOGIN OR SIGN UP TO JOIN THE DISCUSSION
Support Spread
We need the support of our members to keep our forum online. If you find the information on spread useful please consider a donation

Posted by

Ashok Bains
Deepwater Drilling Supt
Discussions: 1
Replies: 3
Related Discussions
Dynamic transmission fluid effects?
BOP pressure test times
Offline testing of safety valves
Casing rams
Well control after drilling with casing
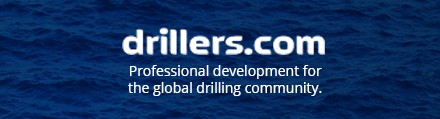
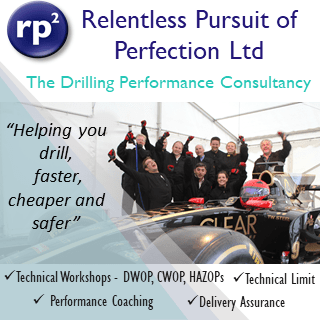