torque reduction with centralised casing string
11 October 2017 Is there a way to quantify surface torque reduction when running a well centralised casing string (80% stand off). How to evaluate the rotational friction factor reduction when adding rigid centraliser to a casing string7 Answer(s)
PLEASE LOGIN OR SIGN UP TO JOIN THE DISCUSSION
Support Spread
We need the support of our members to keep our forum online. If you find the information on spread useful please consider a donation

Posted by
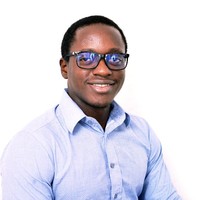
Mike Tony Chembou
Drilling Engineer
Discussions: 3
Replies: 3
Related Discussions
vam thread
Buoyancy Assisted Casing Equipment
10 3/4" Casing Coupling Clearance
Keeping People off Casing
External coating of surface casing
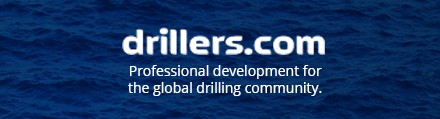
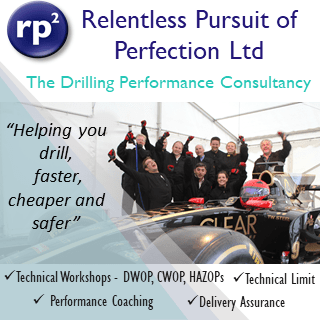