Use of drilling stand
22 June 2011 Hi folksWe are having a heated debate at our Workshop about whether or not we should use a drilling stand (c/w 15k FOSV) for our HPHT well.
The discussion hinges around the potential need to use a kill/kick assy, which will need to be M/U to the drillstring.
In the event of needing to use the kill/kick assy, it's essential that there are suitable barriers on the inside of the drillstring prior to breaking off the top-drive. We discussed the (relatively) common practice of using non-ported double floats in the drillstring .. but these are generally untested and so do not constitute a barrier.
So, the question is :
1. What does your company do and why ?
2. Is there a way to test the floats such that they can be considered a barrier ? (one idea that springs to mind is a test against pipe rams and the casing before drilling out the shoe, but this cannot be done for subsequent assemblies).
3. What about coring assemblies ?
Right, over to you all.
Kind regards
Dave
9 Answer(s)
PLEASE LOGIN OR SIGN UP TO JOIN THE DISCUSSION
Support Spread
We need the support of our members to keep our forum online. If you find the information on spread useful please consider a donation

Posted by
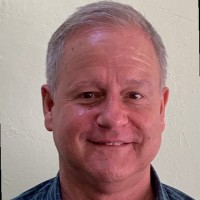
Dave Taylor - SPREAD Moderator
Managing Director (rp-squared.com)
Relentless Pursuit Of Perfection Ltd.
Discussions: 232
Replies: 347
Related Discussions
Rig Personnel Requirements
Ultra HTHP drilling solution
Minimum Rig Standards for drilling HPHT wells
Shutting in the well on a jack-up : Annular or Pipe Rams
Pipe-conveyed logging vs. conventional
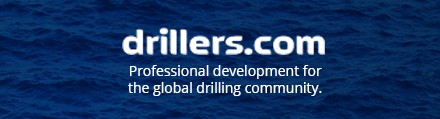
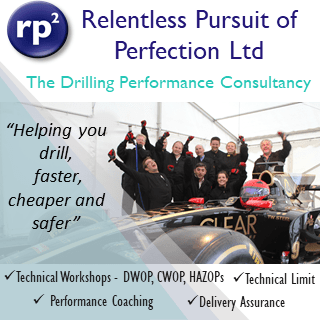