Adjustable Gauge Stabilizer & Motor BHA
20 January 2014 Does anybody in the forum have experience running a steerable motor and an Adjustable (or Variable) Gauge Stabilizer in the same BHA? The idea is to drill a long tangent section and adjusting the inclination using the AGS/VGS and correcting the left/right walk using the steerable motor. I would be interested to know the results. Good, bad or otherwise. I'd also like to know the tool configuration. AGS above or below the motor.Thank you all in advance for your support & expertise.
6 Answer(s)
PLEASE LOGIN OR SIGN UP TO JOIN THE DISCUSSION
Support Spread
We need the support of our members to keep our forum online. If you find the information on spread useful please consider a donation

Posted by

Doug Ellis
SDE
Discussions: 3
Replies: 1
Related Discussions
Avoiding Stick Slip
Jars
Jars Jars Jars
BHA Inspection Criteria
XT 57, Tight Drillpipe Connections
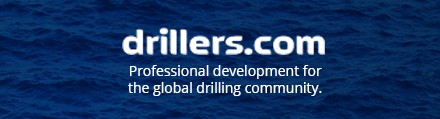
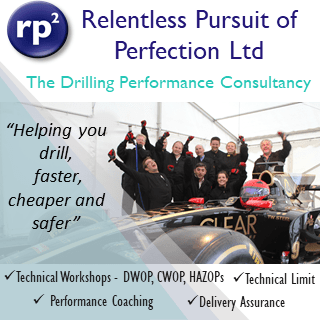