Displacing liner cement with water to suspend
14 May 2008 ”œWe are considering a liner job where we will displace the cementwith inhibited seawater, release from the running tools and then
displace the casing x drillpipe-running-string annulus to seawater
The reservoir is gas-filled at normal pressure.
Tools would be conventional liner running equipment (no inner
string) with weight-set liner-top packer; wiper plugs are installed
at liner top and sheared out when the drillpipe dart exits the
stinger at liner top
Please can anyone provide information on jobs done and/or planned,
in particular addressing :
Well control considerations
Contingencies in case running tool leaks during cement job and
places well in under-balanced situation during cement job
Tools and procedures to allow us to take the next leap forward and
OMIT a cased-hole clean-up run
6 Answer(s)
PLEASE LOGIN OR SIGN UP TO JOIN THE DISCUSSION
Support Spread
We need the support of our members to keep our forum online. If you find the information on spread useful please consider a donation

Posted by

Bob Anderson
Performance coach
Relentless Pursuit Of Perfection Ltd.
Discussions: 2
Replies: 3
Related Discussions
Light Weight Cement for Structural Casing
Cementing 30" With No Vent Valve
Cementing through Tesco Casing Running Tool
Cement mule shoe
Cementing 30" cond (subsea) without an inner string
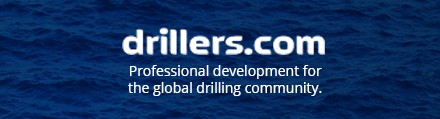
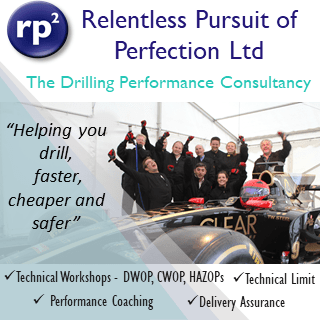