External coating of surface casing
14 June 2009 Hi,Here in Oman we have a highly saline shallow aquifer (7000-10000 mg/l chlorides) down to around 700 m which has also contained H2S in some of our appraisal wells. We currently drill this in 17-1/2" hole and case with 13-3/8" L-80 casing. Best practice here is to ensure cement to surface, but the zone is also prone to severe or total losses, and top-up jobs are routine so an inadequate cement sheath is more or less inevitable, raising the possibility of long-term corrosion of the 13-3/8".
We are contemplating mitigating this risk on our development wells by using externally coated casing so we were wondering if anyone know what options are available, if there are any limitations, price to apply, ease of application etc and also experiences people have with using coated casing to protect from shallow aquifers. We would also like to hear if anyone who has a similarly corrosiove shallow aquifer has had any corrosion issues - timescale, consequence etc - because on our appraisal well the 13-3/8" casing is not protected so we would like to understand the long term integrity risk.
Regards,
Doug Noble
SDE, BG-Oman
Documents uploaded by user:
2 Answer(s)
PLEASE LOGIN OR SIGN UP TO JOIN THE DISCUSSION
Support Spread
We need the support of our members to keep our forum online. If you find the information on spread useful please consider a donation

Posted by

Douglas Noble
Contractor P&A SDE
Discussions: 8
Replies: 1
Related Discussions
vam thread
Buoyancy Assisted Casing Equipment
10 3/4" Casing Coupling Clearance
Keeping People off Casing
Electronic drifting of Tubulars
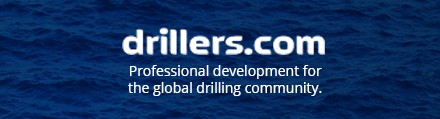
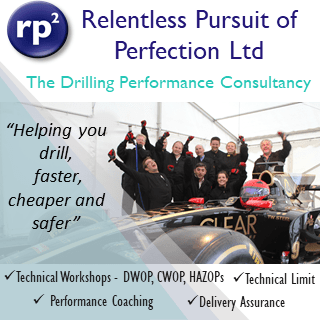