Coring with pipe similar to 34"OD
01 July 2015Dear All
Does anyone used pipe of big OD 34" in drilling with X-O from 34” to Saver sub Connection (6 5/8” Reg).
We would like to have 200 ft of big pipe OD 34" and ID 32.5” to make core and swallow 200 ft. . . .
The 200 ft is very shallow starting from sea bed.
Do you have experience with big pipe, make up torque, thread type, and how many times can be break down the big thread and tight again.
Do you have specification of big pipe to be use in drilling
20 Answer(s)
PLEASE LOGIN OR SIGN UP TO JOIN THE DISCUSSION
Support Spread
We need the support of our members to keep our forum online. If you find the information on spread useful please consider a donation

Posted by

Ahmed salem
DSL (Drill Site Leader)
Discussions: 5
Replies: 33
Related Discussions
Modern rigs; Top drive e-motors
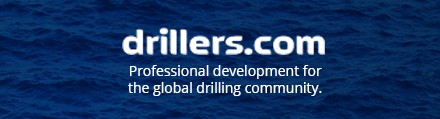
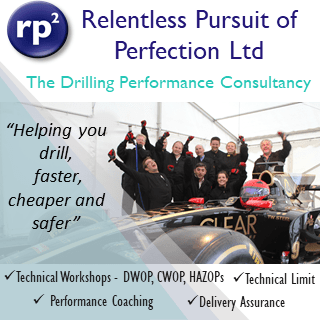