Should we consider Sub Surface Safety Valves as a Barrier?
11 April 2016Good day dear colleagues.
I am included into a team to write a company standard about our ”œBarrier Philosophy”.
Some of us are stipulating that we can use a SCSSSV as a barrier (for workovers, well interventions etc.), once it was positively inflow tested with a zero leak rate. There are companies, but not all of them, whose policies or standards are not allowing that.
Now, is there a good academic reason or
technical explanation for allowing one or the other?
I would like to get your opinion on that subject. Also, if you can´t give me a good academic reason or technical explanation to go for one or the other, could you tell me how your company is dealing with this question and who that company would be?
Thank you very much for your time spent on reading this question already now!
Regards,
Heiko.
16 Answer(s)
PLEASE LOGIN OR SIGN UP TO JOIN THE DISCUSSION
Support Spread
We need the support of our members to keep our forum online. If you find the information on spread useful please consider a donation

Posted by

Heiko Fuchs
Well Services Manager
Discussions: 3
Replies: 4
Related Discussions
Dynamic transmission fluid effects?
BOP pressure test times
Offline testing of safety valves
Casing rams
Well control after drilling with casing
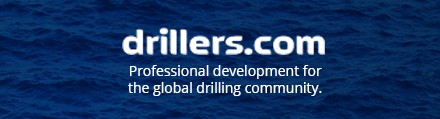
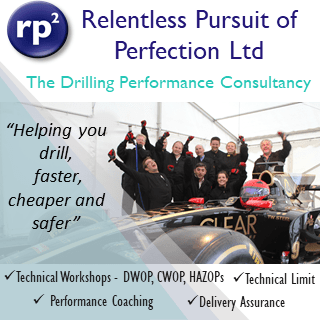