Loss of Grease Seal
17 February 2019Hi All!
Recently we had a big problem with 7 days NPT - loss of
grease seal during PLT.
We rigged up WL PCE (cable cutter, triple BOP, lubricator,
grease injection system and stuffing box) rated for 15K. The problem began as
we start to run, the weight of the tool was not heavy enough to overcome the wellhead pressure,
so we closed the downhole valve, released the pressure and ran the tool. At the
halfway, we pressure up the tubing to equalize at the downhole valve (DV) and open it. Later
we noticed the loss of grease from the return line and gas coming from the top
of PCE. Stopped the run, closed the stiffing box but could not managed to
regain the grease seal - gas was coming from the return. Pulled the tool above
the DV and closed the well at the DV.
Then we checked all flow tubes, changed the grease, tested
the grease injection pump but the next two runs were also unsuccessful - always
the loss the grease seal... The service company at this moment cannot explain why
we are losing the seal. Taking the grease as the main source of problem.
Now we planning to run the tools on slickline as the temporary decision.
Has anybody had a such problems and what was the solutions?
5 Answer(s)
PLEASE LOGIN OR SIGN UP TO JOIN THE DISCUSSION
Support Spread
We need the support of our members to keep our forum online. If you find the information on spread useful please consider a donation

Posted by
Askhat Burlibayev
Hd of Well Testing
Discussions: 10
Replies: 13
Related Discussions
Dynamic transmission fluid effects?
BOP pressure test times
Offline testing of safety valves
Casing rams
Well control after drilling with casing
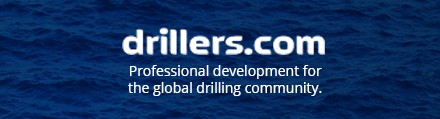
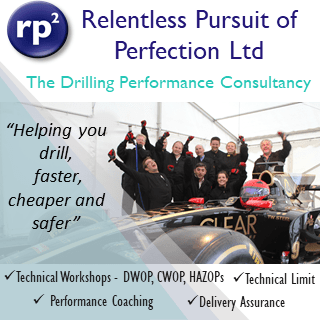