Use of Eccentric/Reamer/Ratchet Casing Shoes When Pipe Rotation Not Possible
01 April 2019Hello
After some issues getting our 13 3/8” casing strings to bottom (due to suspected ledges), we experimented with a couple of different casing shoe designs. Initially we went with conventional shoes but then moved on to eccentric pilot guide shoes and have discussed running reamer shoes, but we do not have the ability to rotate our casing string due to the design of the subsea casing hanger and wellhead system. To provide context we are drilling in about +/- 4,500’ of water building in our 17 ½” section from around 30° at +/- 6,500’ MD up to 90° by around 9,000’ MD.
1) As we cannot rotate the casing I feel we are not getting much benefit of either an eccentric nosed or reamer shoe and furthermore if the nose of the tool is orientated to the low side of the hole it may actually be a hindrance in terms of passing any obstructions. It has been suggested that orientate the nose of the shoe to the high side of the hole when we run it through the rotary as in theory it should not rotate and stay pointed to high side.
2) One of the other options we have considered is the use of an indexing or ratcheting shoe which self-orientates down the hole by setting down on bottom then picking back up. I have had some feedback from our N American drilling teams that they have had issues drilling these out, but I would like to have a broader offset.
Does anyone have any feedback on the above points that they would like to share?
Thanks
Neil Deeney
8 Answer(s)
PLEASE LOGIN OR SIGN UP TO JOIN THE DISCUSSION
Support Spread
We need the support of our members to keep our forum online. If you find the information on spread useful please consider a donation

Posted by

Neil Deeney
Drilling and Completion Superintendent
Society of Petroleum Engineers
Discussions: 4
Replies: 7
Related Discussions
vam thread
Buoyancy Assisted Casing Equipment
10 3/4" Casing Coupling Clearance
Keeping People off Casing
External coating of surface casing
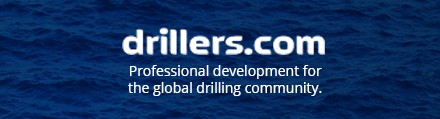
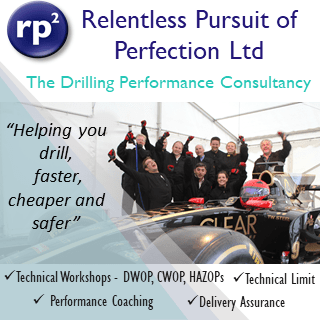