Barriers at Xmas Tree (to break containment)
12 June 2019Dear all
We are preparing for a complicated snubbing fishing programme and we have just received a request that we'd like the members opinion on.
We are preparing for a complicated snubbing fishing programme and we have just received a request that we'd like the members opinion on.
- The GAS well is compromised with a plugged completion. Potentially 6000 psi surface pressure.
- We are being requested to break the wing valve off the tree to rotate an instrument block.
- There are no spares and no people to assist
Question: If we test the LMV from above with water and keep it closed and then test the UMV with water from above does that constitute an acceptable double barrier?
I feel not but………I may be wrong?
Testing gate valves from the wrong side – is that considered an acceptable barrier to permit breaking off the wing valve? This is a gas well and we are testing with water.
As usual it is not as straightforward because we have fish and a plugged completion ………12 months ago. And nobody has a clue what state the well is in now.
We are concerned about breaking the tree integrity, because we can foresee potential damage to the ring groove and we have no spares!
I would be interested to hearing opinions on what can be accepted as barrier.
I need an opinion ASAP, please.
15 Answer(s)
PLEASE LOGIN OR SIGN UP TO JOIN THE DISCUSSION
Support Spread
We need the support of our members to keep our forum online. If you find the information on spread useful please consider a donation

Posted by

Ian Brown
Consultant
Discussions: 2
Replies: 11
Related Discussions
Dynamic transmission fluid effects?
BOP pressure test times
Offline testing of safety valves
Casing rams
Well control after drilling with casing
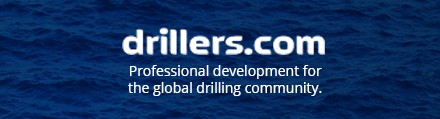
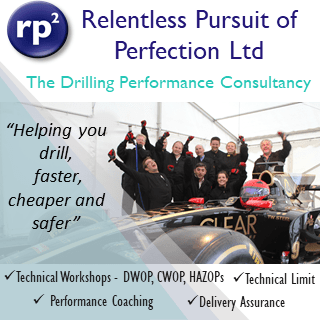