Kick Tolerance Thresholds
01 August 2019I am currently updating the Kick Tolerance section of our well control manuals and I would like to know your thoughts on acceptable kick tolerance thresholds by hole size.
We have a minimum requirement of 25 bbls kick tolerance for 12¼” and 8½” holes. If the well design does not permit the circulating out of an influx of this size using the driller’s method (and its attendant pressures), a deviation/dispensation from our Well Control policies is triggered and additional measures/mitigations are required e.g. Installation of EKD, implementation of 'Level 2' alertness on the rig e.t.c.
We also differentiate between exploration and development wells - 25bbls to 50bbls ktol requires our attention for exploration wells but not for development wells. Our justification for this pertains to the fact that by their nature, exp wells have more uncertainties with respect to geology, formation pressure prognosis and well bore behaviour.
My questions are:
- Where did this “25 bbls” figure originate from?
- What is an acceptable scientific basis for determining
what a standard threshold K-tol should be for a particular hole size?
- What is your company position on K-Tol thresholds and how do you handle deviations?
I heard about a "maximum 300 ft of influx height" rule of thumb and performed some rudimentary analysis with volumes and capacities. I could not find a discernible pattern with either pipe or no pipe in the hole for both hole sizes. at no point was 300ft = 25bbls
I don't like ‘rules of thumb’, so I'm hoping this forum can help me.
Looking forward to your responses.
Ade
19 Answer(s)
PLEASE LOGIN OR SIGN UP TO JOIN THE DISCUSSION
Support Spread
We need the support of our members to keep our forum online. If you find the information on spread useful please consider a donation

Posted by
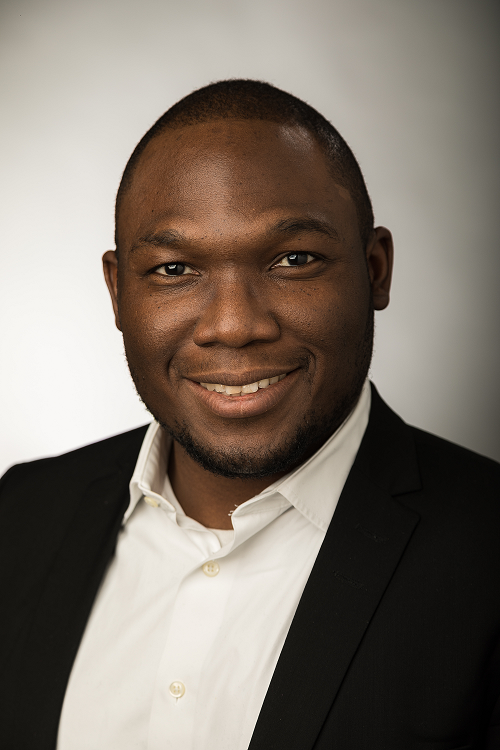
Adebowale Solarin
Drilling Support Superintendent
Discussions: 2
Replies: 9
Related Discussions
Dynamic transmission fluid effects?
BOP pressure test times
Offline testing of safety valves
Casing rams
Well control after drilling with casing
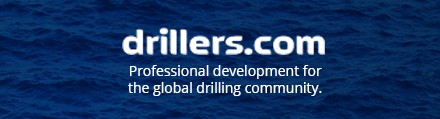
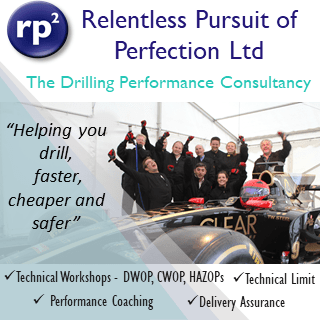