Tubing Leak Mill End - CWSD
15 November 2019We had a 4.5" Vam Top 12.6lb/ft CWSD tubing leak on a recent completion, identified after running a leak detection tool. We kept the leaking connection in tact on completion pull and pressure tested it showing the mill end to be leaking not the field end.
The Mill end was torqued at the mill to 106% optimum torque, the tong jaws grip pipe to pipe so torque goes through field and mill end. Has anyone seen something similar, particularly with Cleanwell Semi-Dry?
There are a number of other issues and human factors here but no conclusive outcome as yet. Been good to hear from the industry about similar situations, although I wouldnt wish it on anyone.
7 Answer(s)
PLEASE LOGIN OR SIGN UP TO JOIN THE DISCUSSION
Support Spread
We need the support of our members to keep our forum online. If you find the information on spread useful please consider a donation

Posted by

Grant MacKinlay
Senior Completion Engineer
Discussions: 2
Replies: 3
Related Discussions
Welltesting .. in daylight hours only ?
ESP's v Gas Lift
Experience with control-line clamps
Injection valves
Annular Safety Valves
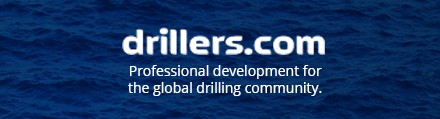
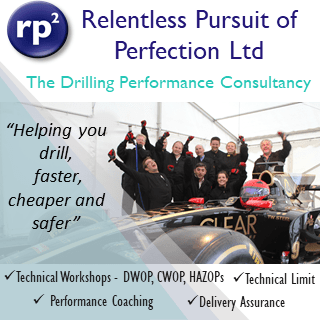