Drill Curve Generation and Analysis
03 April 2020 General question to the group; I've been downloading Pason (Drilling Depth Data) for the last 20years and then plotting it in Excel.There has to be a better way to simply analyze drill curves and identify Non-Productive time, Pacesetters, Interval Problems Etc?!?!
Our daily reporting system is CAODC tour sheets and WellView.
3 Answer(s)
PLEASE LOGIN OR SIGN UP TO JOIN THE DISCUSSION
Support Spread
We need the support of our members to keep our forum online. If you find the information on spread useful please consider a donation

Posted by

Jeff Gerlitz
....
Discussions: 1
Replies: 0
Related Discussions
Basics of Slot Recovery
UBD Flow Modelling
Hole cleaning in UBD
Well Expediture
Recommendation for Casing & Drillstring Design
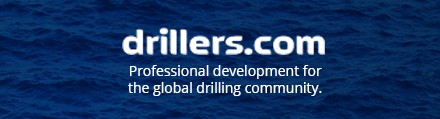
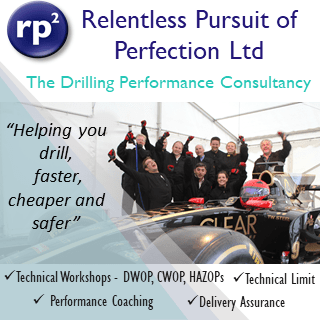