Mitigation plans for tubing buckling during production
12 May 2020 Dear community,We would value your opinions, thoughts and comments with regards to mitigation plans for tubing buckling during production.
We plan to drill and complete HPHT and deep multi-lateral gas well with 1 string 2 packer like attached well schematic.
The first priority for this well is to be able to produce from each leg (zone) selectively for the productivity evaluation though the commingle production will be done mostly. The base plan is to install a sliding sleeve at the junction and a landing nipple at the tubing edge, and to change the production leg by slickline operation (open/close sliding sleeve, set/retrieve plug).
However, based on the experience of existing wells in this field, buckling is the biggest concern due to the hot produced fluid and it might be difficult to do the slickline operation even after a short period shut-in like ~1week.
The well specifications/conditions are below:
- Location: Onshore
- Reservoir Fluid: Gas
- Reservoir(s) Depth: ~16,000ft
- Reservoir Temp: ~400degF
- Wellhead Temp during Production: ~200degF
- Sliding Sleeve Depth (Inclination): ~15,200ft (40-50 degree)
- Calculated Tubing Elongation during Production: ~16ft@3-1/2" tubing
We've searched the mitigation plan in terms of completion design and found the followings so far:
- Install an expansion joint which compensates for tubing movement above the upper packer.
- Install a large bore system and a long seal assemblies at tubing locator which allows for a floating seal to compensate for tubing elongation or contraction.
- Complete with a larger size of tubing above the upper packer to help slickline assembly run easier to below the upper packer (the sliding sleeve and landing nipple).
- Install remote tools (sliding sleeve and valve) and remove slickline operations.
- Is there any other mitigation plan in terms of completion design?
- Which one is the best practice based on your experience?
Best Regards,
Hiro
Documents uploaded by user:
7 Answer(s)
PLEASE LOGIN OR SIGN UP TO JOIN THE DISCUSSION
Support Spread
We need the support of our members to keep our forum online. If you find the information on spread useful please consider a donation

Posted by

HIRO KONO
Well engineer
Discussions: 2
Replies: 2
Related Discussions
Welltesting .. in daylight hours only ?
ESP's v Gas Lift
Experience with control-line clamps
Injection valves
Annular Safety Valves
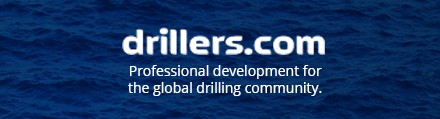
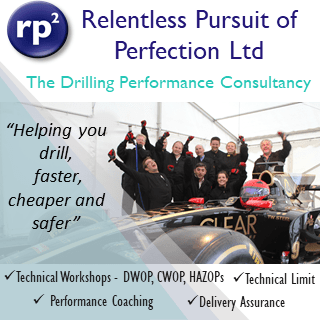