Tubing pressure test
22 January 2021 Dear Sirs,I really need your help of how the new or used tubing hydro statically tested while it runs in the hole?
Thanks and Best Regards
9 Answer(s)
PLEASE LOGIN OR SIGN UP TO JOIN THE DISCUSSION
Support Spread
We need the support of our members to keep our forum online. If you find the information on spread useful please consider a donation

Posted by

Mohammed Ali
Student
Discussions: 1
Replies: 0
Related Discussions
Cutting Tubing in Compression
Well Kill
Slot Recovery
Workover of subhydrostatic wells in offshore oil field
ROV Pinch Ring's Option to Re-Establish the Guideline to Guide Posts
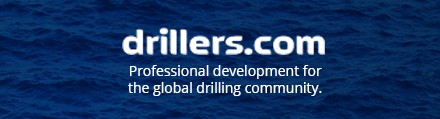
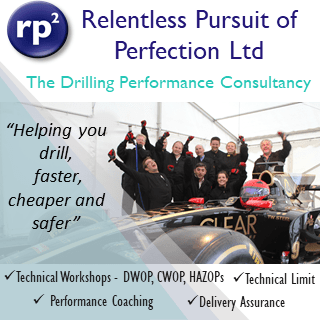