Float Equipment for 10k psi Pressure Tests
11 May 2010 Hello All,In the Western Canadian Horn River Basin Shale Gas play we are having problems with leaking shoe tracks on our production casing when we test the casing to 10,000 psi.
The casing string is a tapered string of 5 1/2", P110, 20 ppf and 5 1/2", T95, 23 ppf casing with JFE bear premium connections. We have ran both 3 joint and 5 joint shoe tracks. FTD is 4700m (15,400 ft) and TVD is 2450m (8000 ft) with roughly 1800m (5900 ft) horizontal length. The bottom hole temperature is 140 deg C (285 deg F).
We used a Weatherford latch down top plug capable to 10k psi pressure tests, and we are bumping at calculated volume so we should have cement in the shoe track. After the initial bump, we increase the pressure to 35 MPA (5,000 psi) with no problems. Unfortunately, we cannot go higher with the drilling rig ... but this test confirms the plug has landed (and hopefully latched).
After the drilling rig moves off, we pressure test the casing to 10,000 psi to prove integrity for the upcoming frac jobs (3 weeks after cement job). Unfortunately, roughly 50% of the wells on our last pad have leaked at the shoe track. Both the cement and the plug seem to be failing.
Does anyone have recommendations for a top cement plug capable of 10,000 psi pressure tests in a high temperature environment? Any recommendations on shoe track length in this size and length of hole (is 3 or 5 jts sufficient or should we run more)? Any other idea's on how to get a competent shoe?
Thanks,
Mike Pottle
Drilling Engineer
Horn River Basin - Shale Gas
Nexen Inc.
801 - 7th AVE SW
Calgary, AB, Canada T2P 3P7
3 Answer(s)
PLEASE LOGIN OR SIGN UP TO JOIN THE DISCUSSION
Support Spread
We need the support of our members to keep our forum online. If you find the information on spread useful please consider a donation

Posted by

Mike Pottle
Drilling Engineer
Discussions: 1
Replies: 0
Related Discussions
Light Weight Cement for Structural Casing
Cementing 30" With No Vent Valve
Cementing through Tesco Casing Running Tool
Cement mule shoe
Displacing liner cement with water to suspend
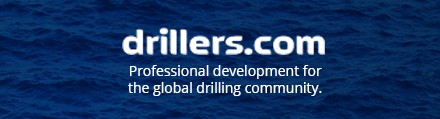
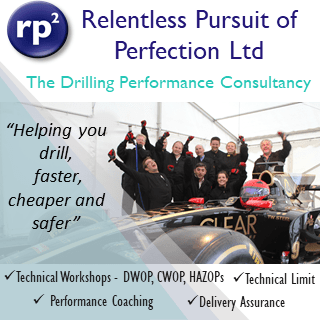