7" liner cementing with very narrow pressure margin
** Updated this discussion with a supplementary question, to cover an actual situation that developed recently with one of our clients ** (Dave Taylor 6-Jun-2015) .. see Response Number 4Gday,
I have only 1.2ppg drilling margin in my 8-1/2" hole section and will set the 7" liner across the section for DST.
My final MW will probably be 18ppg and the cementer has provided a design of minimum 18.5 ppg slurry. The problem is my offset frac gradient is at 18.6-18.7ppg!
Anyone has encountered such problem? .. what did you do about it, and what was the final outcome ?
Noor Nordin
Drilling Engineer
Petronas, Malaysia
8 Answer(s)
PLEASE LOGIN OR SIGN UP TO JOIN THE DISCUSSION
Support Spread
We need the support of our members to keep our forum online. If you find the information on spread useful please consider a donation

Posted by

Noor Nordin
Well Business Excellence Lead
Discussions: 3
Replies: 7
Related Discussions
Light Weight Cement for Structural Casing
Cementing 30" With No Vent Valve
Cementing through Tesco Casing Running Tool
Cement mule shoe
Displacing liner cement with water to suspend
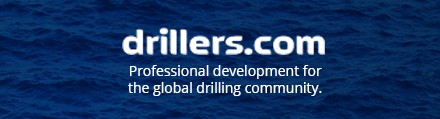
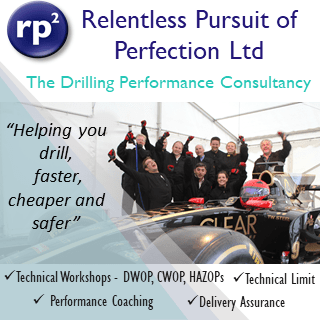