Effect of Applied Pressure at surface during cement hardening
19 July 2010 AllNeed your advice
Does anyone here experienced with the applied pressure at surface during cementing hardening. The reason behind this is we have a better reading of cement log (USIT) rather than conventional i.e. close cementing valve and WOC without pressure. In addition, the sub-surface team is pleased with the way we have as the oil is produce with minimal water-cut.
There is no different cement recipe that we used except the mechanical effort as we mentioned above.
I would be grateful if you can advice us with sound engineering background
Regards,
Gustioro
Medco Indonesia
3 Answer(s)
PLEASE LOGIN OR SIGN UP TO JOIN THE DISCUSSION
Support Spread
We need the support of our members to keep our forum online. If you find the information on spread useful please consider a donation

Posted by

Gustioro Gute
Head of Front End Wells
Discussions: 1
Replies: 0
Related Discussions
Light Weight Cement for Structural Casing
Cementing 30" With No Vent Valve
Cementing through Tesco Casing Running Tool
Cement mule shoe
Displacing liner cement with water to suspend
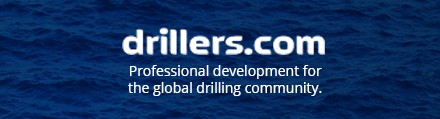
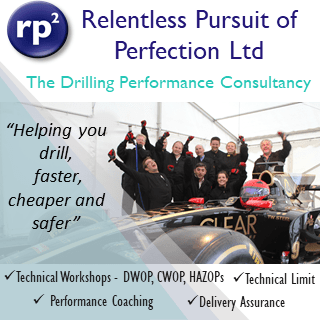