Pyrophoric Shale on Tubulars
04 April 2012 Hello all,Has anyone had experience of pyrophoric shale found on/in recovered tubulars? Has this situated ever occurred in the North Sea? If not, then has it occurred anywhere else in the world?
How is it detected? And if you can't detect it, how do you know you have it?
Finally, what is the best way to tackle it and return the tubulars to shore?
Any advice would be greatly appreciated. Thank you all.
5 Answer(s)
PLEASE LOGIN OR SIGN UP TO JOIN THE DISCUSSION
Support Spread
We need the support of our members to keep our forum online. If you find the information on spread useful please consider a donation

Posted by

Steve Armstrong
Well Engr
Discussions: 1
Replies: 1
Related Discussions
Oxygen/Acetylene Generators
Exploding Battery
Floatation fo Bunkering Hoses
SIMOPS Matrix - Concurrent Drilling, Construction & Production
Wells Register
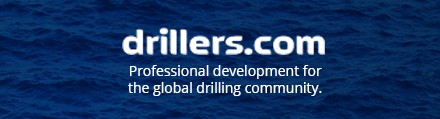
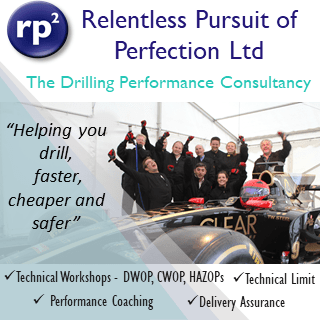