Drilling shoetrack with 1.15 deg bend in motor (and PDC bit)
Hi folksAt a recent DWOP, the draft programme being reviewed had a BHA with a 1.15 degree bend in the motor. A PDC bit is planned.
We discussed the possibility of severe damage to the bit whilst drilling the shoetrack, and also challenged the need for such an aggressive bend in what amounts to a vertical well; bend was proposed to give some capability to correct inclination.
As usual, there were as many opinions as there were people sitting at the table.
We're interested to hear of members' experiences in this regard.
With kind regards.
Dave Taylor
24 Answer(s)
PLEASE LOGIN OR SIGN UP TO JOIN THE DISCUSSION
Support Spread
We need the support of our members to keep our forum online. If you find the information on spread useful please consider a donation

Posted by
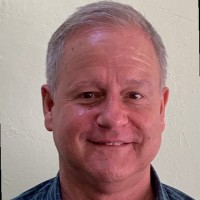
Dave Taylor - SPREAD Moderator
Managing Director (rp-squared.com)
Relentless Pursuit Of Perfection Ltd.
Discussions: 224
Replies: 332
Related Discussions
Drilling 8 1/2" hole out of 20" shoe
37" HoleOpeners
Flexjoint wearbuushings
Clearing site for landrigs
Thru tubing fishing
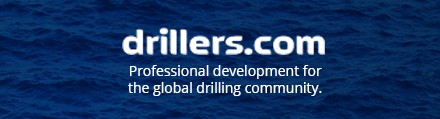
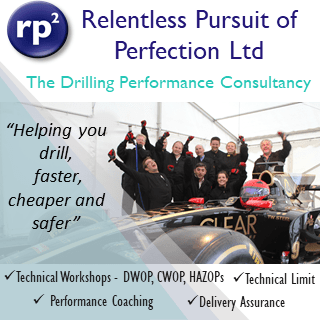