Fatigue analysis with very short fatigue life
22 April 2013 Fatigue analysis seems to now be undertaken more commonly for subsea exploration / appraisal (P&A) wells in the North Sea. The results of a fatigue analysis we've had done are suggesting a requirement for much heavier equipment than expected or has been used in the past. It appears some operators are now using heavy conductor for fatigue resistance (i.e. 36" x 2" instead of 30" x 1.5") and wellhead equipment in similar water depths (400ft), but other operators nearby in similar water depths have much lighter equipment. Our concern is that higher specs (including weld quality and extension joint length) could restrict our ability to source equipment. Have those of you who have had similar experiences with fatigue modelling found any learnings that can be taken to mitigate against potentially overdesigning the well due to fatigue modelling?It could be that this well actually does require heavy equipment, but fatigue analysis has a reputation for being a bit of a dark art with large safety factors (e.g. DnV safety factor of 10); are there any learnings yet from actual measurements made against modelling?
Regards,
7 Answer(s)
PLEASE LOGIN OR SIGN UP TO JOIN THE DISCUSSION
Support Spread
We need the support of our members to keep our forum online. If you find the information on spread useful please consider a donation

Posted by

Arun Patel
Drilling Engineer
Discussions: 3
Replies: 7
Related Discussions
Deepwater Wellhead Systems Review
Bullseyes?
Subsea Wellhead - seal assembly retrieval
Subsea wellhead rating
Drilling Riser VIV - old paper
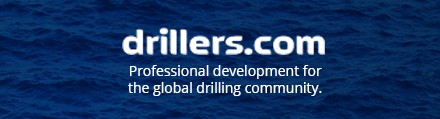
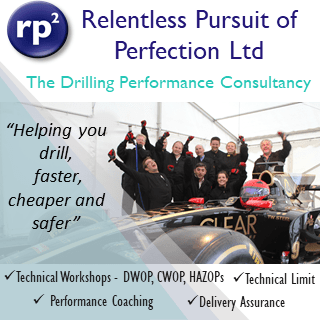