Overbalanced drilling - optimizing HSI and impact force or jet velocity
20 October 2015We just ran a 6'' Talon bit to drill horizontal - the formation is weak and we run highly overbalanced with MW 1.45 and Formate mud - geomechanics study advised high MW. SPP is limited and the HSI planned for the PDC is just 1.0 HP/in2.
Because we drill highly overbalanced ROP will be slowed down rapidly - cuttings will be held on bottom - "chip hold down" effect - for my understanding impact force and HSI would help to prevent drilling the same chips again and again - of cause not with significant ROP increase because overbalanced pressure effect is exponential -
http://www.drillingcontractor.org/shale-drilling-reaps-efficiency-gains-from-mpd-pressure-control-23264
But if we drill at 2.0m/h instead of 1.7m/h for 570m we will save 2 days. Are there any papers or publications showing that even with high overbalance (300 bar above pore pressure) HSI and impact force should be high as well or will better bit hydraulics not help to get better ROP in this case.
7 Answer(s)
PLEASE LOGIN OR SIGN UP TO JOIN THE DISCUSSION
Support Spread
We need the support of our members to keep our forum online. If you find the information on spread useful please consider a donation

Posted by
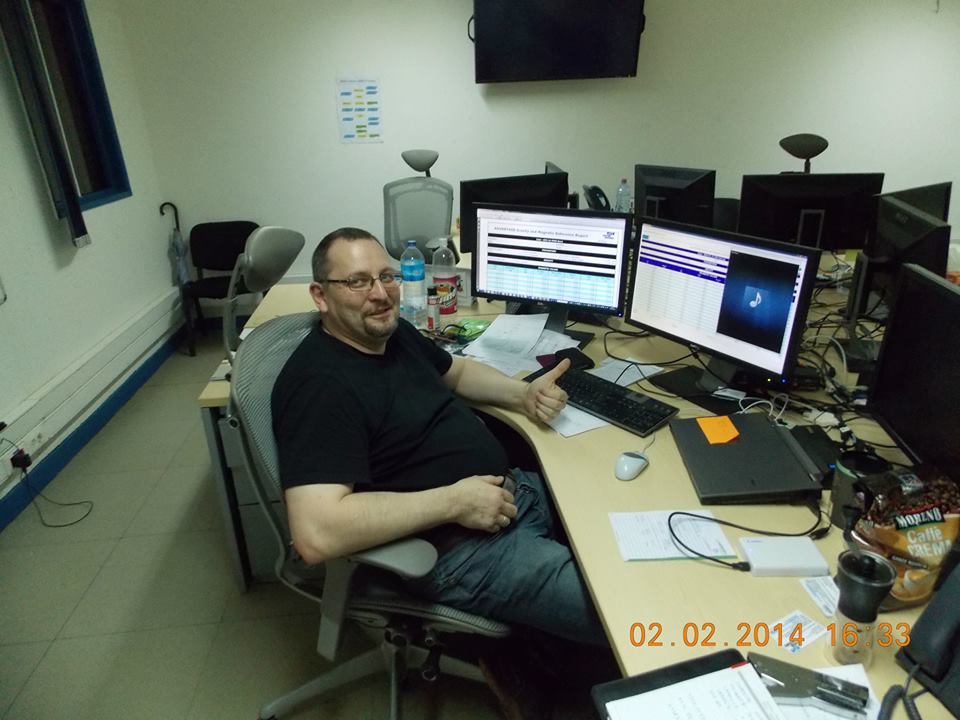
Peter-Joern Palten
Senior Drilling Engineer
Discussions: 7
Replies: 45
Related Discussions
Sacrifice fluid (water) in PMCD HPHT
Underbalanced Torque and Drag
Rotating Control Heads
RMR system for the wells in >600m water depth
Regarding Top kill -recommended practice,successes or anything similar
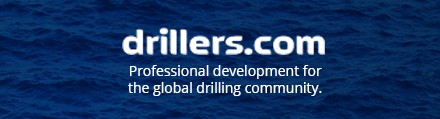
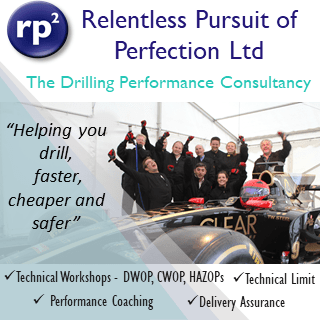