Surface Torque maxing out
15 December 2015Folks,
Any pointers will be greatly appreciated.
Issue: Surface rotary torque maxes @ 30,000 ft-lbs once landed & 2000´ in lateral
Hole size: 8 /2” DP: 5” #19.5 S-135
Profile: surf nudge to 6 deg & bck to vertical”¦KOP ~ 10,000, 10/100 DLS, land 94 deg ~ 11,000, 2-D well, dropping to 92 deg by TD ~ 18000'
Curve & lateral bha: 5 bladed PDC, Motor (2deg fxd bend), MWD, DP---OBM
Torque in vertical: ~16K ft-lbs”¦once we land out torque goes up to ~24K & to ~30K around 2000´ into lateral. Off -btm torque~22K
Can we eliminate hole cleaning as torque goes back up when on btm?...could it buckling?...is it the agressive plan??..any ideas or pointers to check where this excess torque could be coming from?
6 Answer(s)
PLEASE LOGIN OR SIGN UP TO JOIN THE DISCUSSION
Support Spread
We need the support of our members to keep our forum online. If you find the information on spread useful please consider a donation

Posted by

Venkat Chitor
DE
Discussions: 7
Replies: 4
Related Discussions
Drilling 8 1/2" hole out of 20" shoe
37" HoleOpeners
Flexjoint wearbuushings
Clearing site for landrigs
Thru tubing fishing
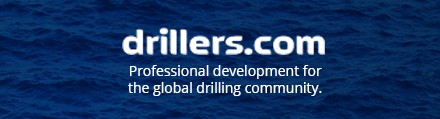
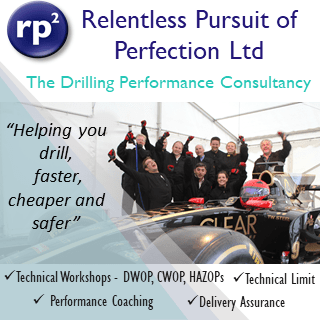