Shock & Vib - BHA related
08 March 2016All,
Trying to optimize intermediate BHA in effort to decrease shock / vibe & would appreciate your thoughts & experience (good / bad) with below...
1) Currently running 8" NMDC, then XO to 6-1/2” DC´s. Would additional 8” DC´s help to minimize shock/vibe by maximizing inertia? Any downsides?...are HW a better alternative?
2) Effectiveness of shock sub or other shock./vibe dampening tools
3) Effect of bit guage length
4) In production section, the effect of slick vs flex NMDC while choosing DCs
5) IBS vs roller reamer effectiveness
Thanks
6 Answer(s)
PLEASE LOGIN OR SIGN UP TO JOIN THE DISCUSSION
Support Spread
We need the support of our members to keep our forum online. If you find the information on spread useful please consider a donation

Posted by

Venkat Chitor
DE
Discussions: 7
Replies: 4
Related Discussions
Drilling 8 1/2" hole out of 20" shoe
37" HoleOpeners
Flexjoint wearbuushings
Clearing site for landrigs
Thru tubing fishing
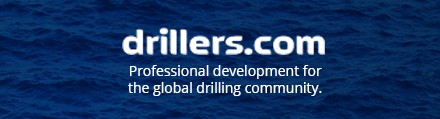
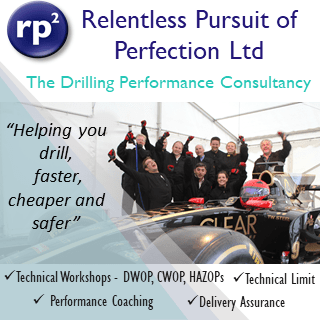