Sodium Silicate mud
10 March 2016 I am wondering about the experiences people have with Sodium Silicate mud.How does it effect down-hole tools?
How to calibrate hydraulic programmes?
Essentially - what are the pros and cons with such a mud system?
7 Answer(s)
PLEASE LOGIN OR SIGN UP TO JOIN THE DISCUSSION
Support Spread
We need the support of our members to keep our forum online. If you find the information on spread useful please consider a donation

Posted by
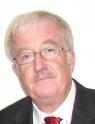
Chris Henderson
Mentor to the youth of our industry
Discussions: 57
Replies: 70
Related Discussions
Using gilsonite as a fluid loss control additive
Extreme Losses in Carbonate
Heating of drilling mud
H2S scavenger level in WBM
High Bottom Hole Temperatures
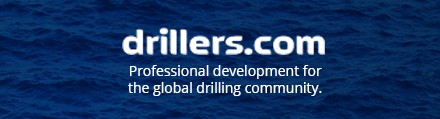
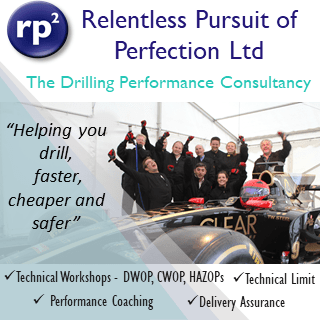