Planning optimal well design: Mitigating risks of drilling through abnormal pressured lenses
22 March 2016This item crops up on numerous well designs, how to mitigate the risk of abnormal pressure lenses particularly in the intermediate/production sections to maintain an optimal well design.
The scene: One offset in the area encountered an abnormal pressure lens, took a kick and the same zone may or may not be present on your location- but can´t be discounted. 9 times out of 10 you don't see anything when you drill them.
Planning: when designing the well do you push on and drill through to next section TD accepting the potential performance risks, high overbalance, low ROP, losses, unable to reach TD or do you deal with potential abnormal pressure lens and isolate it requiring extra string, cost and time.
I would like to know if there is a more pragmatic approach and understand the merits of particular strategies used by
members in the group.
Some of
the risks:
1) high
overbalance - subsequently performance risks drilling ahead
2) hole
size (17-1/2”)- ability to dynamically kill abnormal pressured lens
3) kick
tolerance (surface casing)
Mitigating
Strategies:
1) Accept high overbalance and drill ahead (high risk of low ROP), set decision tree options Drill ahead, set liner/
casing could be planned based on depth, ROP and time.
2)
Plan to drill through and
case off with extra string/liner,
lower MW
3)
Plan to drill through take
pressure points confirm yes/no pressured and adjust MW
4) Push surface casing as deep as possible or
extra string for kick tolerance
5) Drill different hole size (slim) to
dynamically kill it- dedicated pilot hole
6) Is there any lookahead tools on the market
that can provided added value in the assessment of the lens being abnormally
pressured?
4 Answer(s)
PLEASE LOGIN OR SIGN UP TO JOIN THE DISCUSSION
Support Spread
We need the support of our members to keep our forum online. If you find the information on spread useful please consider a donation

Posted by

Matt Morrison
DS
Discussions: 1
Replies: 1
Related Discussions
running conductor casing
"Green" Casing dope
Cuttings re-injection into gas lifted wells.
Inter Field Cuttings Transportation
Jack up 'Slim hole' finder well design
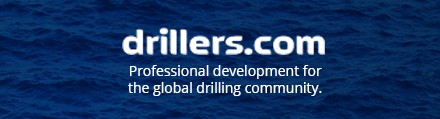
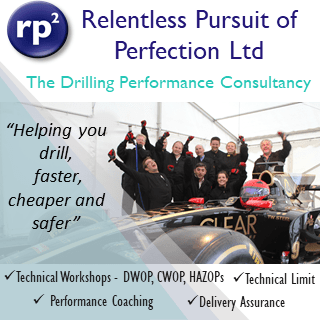