What's the big deal about RDF?
28 June 2017 Hi folksAt the workshops that I'm facilitating, I hear more-and-more these days about RDF (Reservoir Drilling Fluid). I am (kind of) familiar with DIF (Drill-in Fluids) which we were using years ago, but RDF is a fairly new one on me.
My questions are:
- What's the difference between DIF and RDF (if any)?
- What circumstances would make it worthwhile to use RDF?
- What circumstances tend to make it not worthwhile to use RDF?
- What tests and financial-modelling can be applied to determine the cost vs. benefit of these fluids?
- Are there any compelling case histories that show the benefits (or otherwise)?
- If RDF are 'so good' then why isn't everyone using them?
Dave
2 Answer(s)
PLEASE LOGIN OR SIGN UP TO JOIN THE DISCUSSION
Support Spread
We need the support of our members to keep our forum online. If you find the information on spread useful please consider a donation

Posted by
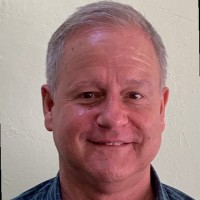
Dave Taylor - SPREAD Moderator
Managing Director (rp-squared.com)
Relentless Pursuit Of Perfection Ltd.
Discussions: 230
Replies: 346
Related Discussions
Using gilsonite as a fluid loss control additive
Extreme Losses in Carbonate
Heating of drilling mud
H2S scavenger level in WBM
High Bottom Hole Temperatures
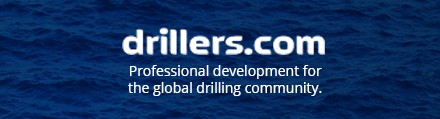
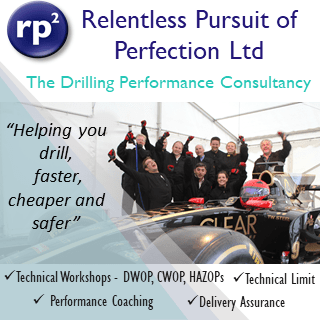