Reverse Cementing
01 February 2018Hi,
we are planning a reverse cement Job for 24" casing run in 28" hole size, the previous casing is 26" - ID - 25"
26" casing setting depth - 2700ft
24" casing setting depth 3650ft.
The Top of cement behind 24" casing is 2300ft. covering a big loss zone.
FG at 24" casing depth 10.5ppg
MW drilling was 9.1 ppg
I appreciate your help understanding what way to go- Conventional cementation or Reverse cementing.
What are the Hi-points or Low points for Both.
What is achievable having good cement bond behind casing covering the loss Zone.
If anyone has case studies , SPE papers kindly share.
Appreciate your help
Thanks & Best Regards,
Hari.
9 Answer(s)
PLEASE LOGIN OR SIGN UP TO JOIN THE DISCUSSION
Support Spread
We need the support of our members to keep our forum online. If you find the information on spread useful please consider a donation

Posted by

Vinod Mahadik
engineer
Discussions: 12
Replies: 10
Related Discussions
Light Weight Cement for Structural Casing
Cementing 30" With No Vent Valve
Cementing through Tesco Casing Running Tool
Cement mule shoe
Displacing liner cement with water to suspend
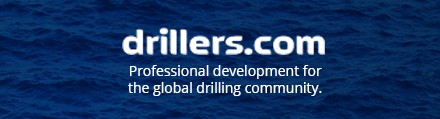
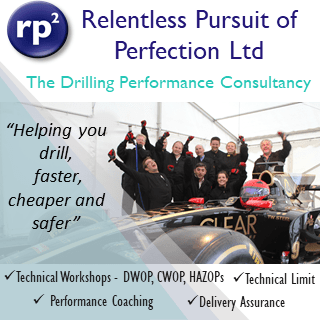