Torque at drill bit
05 March 2018 Spread Community, particularly drill bit experts:I would like to know what the likely torque is directly at the drill bit when drilling a hard formation with a 8½" and 12¼" PDC drill bit, not the surface torque, nor the torque at the top of the BHA, just the torque required by the drill bit itself.
Obviously, there are numerous PDC drill bit designs and types where this drill bit torque requirement is different, but I am looking for the range that the torque might be.
Is it 100's of ft/lbs, or a few 1000's of ft/lbs, it's obviously not 10,000's of ft/lbs or we could not use them on top of what it takes to turn the drill pipe and BHA as well.
If you have any specific data with bit type and formation type it would be great to have that.
Also, if you know the above, do you know how much it differs for reaming through a hard formation rather than drilling 100% of the hole diameter.
Thanks in advance for your input.
5 Answer(s)
PLEASE LOGIN OR SIGN UP TO JOIN THE DISCUSSION
Support Spread
We need the support of our members to keep our forum online. If you find the information on spread useful please consider a donation

Posted by

Paul Howlett
CEO
Discussions: 4
Replies: 142
Related Discussions
Black box diagnostics technology?
Soluble oils for Koomey units
Undereaming/Bi Center Bits
Temporary suspension options (Cased hole retrievab
Ghost reamers
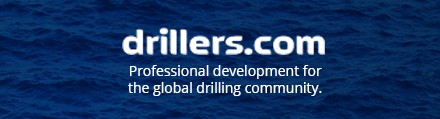
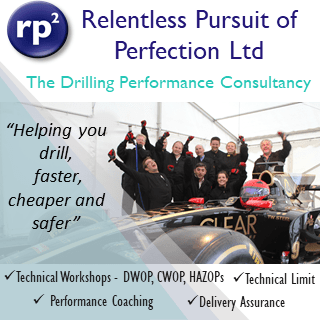