High angle surface casings
13 August 2018Hi All,
I'd like to know what the experience has been designing and drilling shallow extended reach horizontal wells, resulting in high angle surface casings: > 50 degs. This kind of design has been utilized successfully in a couple of wells in the past (before my time) but I'm wondering what kind of risks /areas of concern this would introduce as there is limited information on the older wells.
A summary of the project I'm looking at is as follows:
The project is an infill drilling project from a platform located in circa 32ft-md of water. All the conductors have been pre-installed and at depths 500 - 600 ft-MD. The depths for the reservoir targets are circa 3000ft - 3300TVDss and these have a step out distance from the platform of circa 6000 - 9000ft MD. To achieve the horizontal trajectory design (aligning both the heel and toe), the inclination needs to built quite aggressively from the surface section. Currently the trajectories have been built with 1 - 4.5 deg/100ft in the surface section and slightly higher in the subsequent hole sections. A dril-quip surface well head system: the dual bore 2 step unitized wellhead, is to be utilized for the project.
My main concern is the consequence of the very high surface casing inclinations and the impact on the overall well design. Besides casing wear are there other risks I should be looking at? If so how were these risks mitigated or eliminated. In addition is there any rule for max surface casing inclination.
7 Answer(s)
PLEASE LOGIN OR SIGN UP TO JOIN THE DISCUSSION
Support Spread
We need the support of our members to keep our forum online. If you find the information on spread useful please consider a donation

Posted by

Chike Nwagu
Drilling Engineer
Discussions: 5
Replies: 0
Related Discussions
Milling through a casing collar
With this down turn in our industry are multilaterals a useful well construction technique to reduce costs?
Expert Training Support Offer : How the Latest ERD Innovations Can Benefit Your Deviated Wells
How to remember everything you have ever learned.
Coiled tubing bridge plug milling
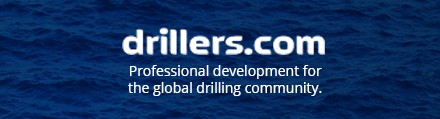
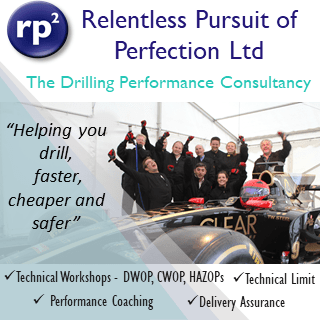