Time limits on pre-loading wiper darts
11 April 2009 At a recent DWOP we facilitated, the topical recommendation to pre-load cement wiper plus/darts came up.This can be the subsea release wiper plugs run below casing hangers and/or liner wiper darts in cement heads.
We know there are potential issues with storing these pre-M/U assemblies due to the fact that the dart may distort.
Please can you share with us your standard practices within your own companies, along with any experiences (bad or good, plus precautions you have taken.
Thankyou
Dave Taylor
12 Answer(s)
PLEASE LOGIN OR SIGN UP TO JOIN THE DISCUSSION
Support Spread
We need the support of our members to keep our forum online. If you find the information on spread useful please consider a donation

Posted by
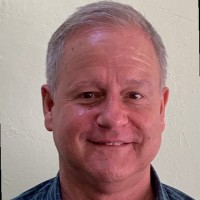
Dave Taylor - SPREAD Moderator
Managing Director (rp-squared.com)
Relentless Pursuit Of Perfection Ltd.
Discussions: 230
Replies: 346
Related Discussions
Light Weight Cement for Structural Casing
Cementing 30" With No Vent Valve
Cementing through Tesco Casing Running Tool
Cement mule shoe
Displacing liner cement with water to suspend
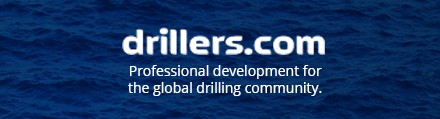
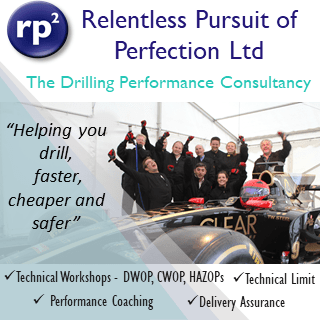