Stabilisers or Reamers.
25 September 2011 Ladies and gentlemen,What are the main criteria you would propose affects the decision to run stabilisers or roller reamers in a BHA design.
My opinions are somewhat outdated I fear and out of touch with the modern tools.
Perhaps you people know better..???
7 Answer(s)
PLEASE LOGIN OR SIGN UP TO JOIN THE DISCUSSION
Support Spread
We need the support of our members to keep our forum online. If you find the information on spread useful please consider a donation

Posted by
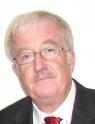
Chris Henderson
Mentor to the youth of our industry
Discussions: 57
Replies: 70
Related Discussions
Avoiding Stick Slip
Jars
Jars Jars Jars
BHA Inspection Criteria
XT 57, Tight Drillpipe Connections
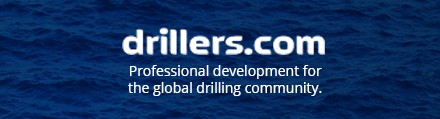
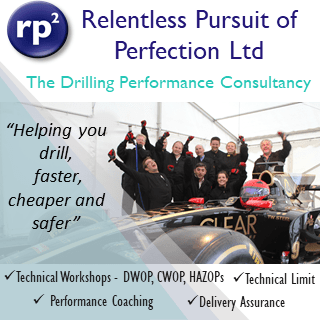