Well abandonment: Pumping cement through XT valves
22 August 2018 Dear members,With well abandonment activity now an increasing part of life, here's one for you to get your teeth into.
Not everyone has the luxury of re-entering SUBSEA wells where the initial Project team had considered the fact that some poor soul(s) would be called upon in later life to re-enter the wells, after cessation of production, and secure them in perpetuity.
Imagine this. (And please don't ask "why").
One of the few options left available to you, before you can remove the (vertical) Xmas Tree (XT), is to secure the lower section of the well with a cement plug as one of the barriers required before you can confidently remove the tree and install the MODU x BOP.. You can access the production tubing, but the tree design (and please don't ask) does not allow anything other than circulation/pumping access to the annulus.
You are able to access the Production bore with pretty much anything that you wish, but concerns about the original design of the tree hub (stresses) has made it 'uncomfortable' for you to confidently deploy the full weight/stress of a conventional LRA/EDP all the way back to a MODU.
So you have been thinking about severing the tubing and 'spotting' a cement plug via a LWI riser system (i.e. no coiled tubing).
This means that you may little choice other than to bullhead cement down the system (down the tubing) and to circulate it into place into the annulus, deep down.
However, this means that the cement will pass trrough the XT.,
Do you see the concern?
So, the million-dollar questions are:
- Have you faced this challenge?
- Have you pumped (bullheaded) cement through the XT valves?
- Did this affect the XT valves?
- If not, why not (what did you do to avoid it doing so?)
- If it did affect them, please tell us about it and what would you do differently?
- What technology exists to get that cement down there without these concerns?
- If you've not come across this (just yet!) but have some great ideas how to beat this challenge, then let us know in this open forum, for the benefit of our industry.
Best wishes
Dave
9 Answer(s)
PLEASE LOGIN OR SIGN UP TO JOIN THE DISCUSSION
Support Spread
We need the support of our members to keep our forum online. If you find the information on spread useful please consider a donation

Posted by
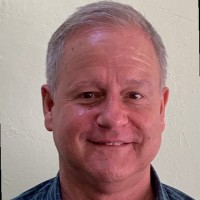
Dave Taylor - SPREAD Moderator
Managing Director (rp-squared.com)
Relentless Pursuit Of Perfection Ltd.
Discussions: 232
Replies: 347
Related Discussions
Relying on shales as annulus barriers
Cement Plugs in CaBr enviromental
Pump and Pull techniques, high angle wellbores.
Well Abandonment - Control Lines
abandonment work
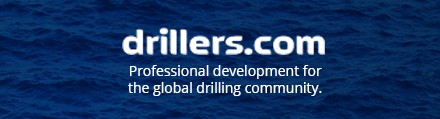
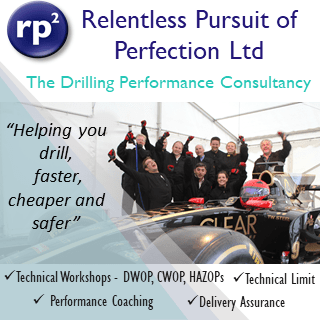