Drill-pipe and casing lengths and threads
10 February 2019 Good morningI have got two questions that I want to share with you and discuss the answer:
1- why the Drillpipes and Casing have not the same length and we have many ranges and even for the same range we find different lengths?!
2- why the drillstring is delivered with different threads and is not made from only one thread?!
Thanks
Dave
4 Answer(s)
PLEASE LOGIN OR SIGN UP TO JOIN THE DISCUSSION
Support Spread
We need the support of our members to keep our forum online. If you find the information on spread useful please consider a donation

Posted by

Sidi Yahia Berrouigat
Drilling Coach / Wewll Control Instructor
Discussions: 12
Replies: 16
Related Discussions
Avoiding Stick Slip
Jars
Jars Jars Jars
BHA Inspection Criteria
XT 57, Tight Drillpipe Connections
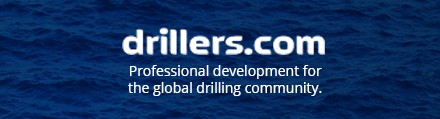
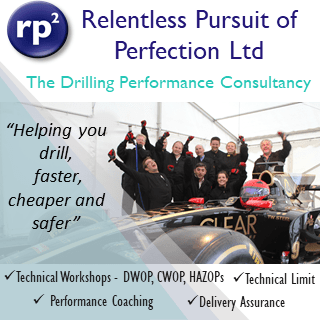