Acquiring data to assist with difficult cement jobs
12 February 2019Dear members
Given some of the close-tolerance wells that are being drilled, a potential customer (in a Major Oil Co) has asked what the industry thinks about the following potential game-changer(s).
Challenge: Can we develop smart technology around the casing running and cement jobs, that could be integrated into the casing that could:
1. Measure and transmit surge pressure whilst lowering the casing
2. Measure the hole caliper (directly or by inference)
3. Measure Borehole breakout analysis
4. Measure annuli pressure build-up
5. Device that accurately determines the volume-to-bump BEFORE the cement job (i.e. whilst circulating to condition the mud).
We would love to hear what you think and especially from those who are working on solutions; we will lift our 'no sales pitch' rule (in this instance) as long as you provide meaningful information in your reply (not just redirecting us to your website).
Thanks
Dave
6 Answer(s)
PLEASE LOGIN OR SIGN UP TO JOIN THE DISCUSSION
Support Spread
We need the support of our members to keep our forum online. If you find the information on spread useful please consider a donation

Posted by
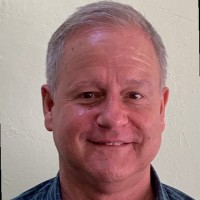
Dave Taylor - SPREAD Moderator
Managing Director (rp-squared.com)
Relentless Pursuit Of Perfection Ltd.
Discussions: 232
Replies: 347
Related Discussions
Light weight corrosion caps
Corrosion Inhibitor delivered in bags
Managed pressure drilling to increase mud weight
Dope-less Connections
Land Rig Site Preparation - Ground Bearing Pressure Problem
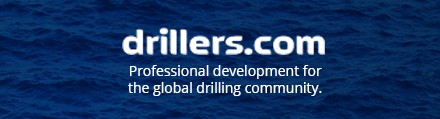
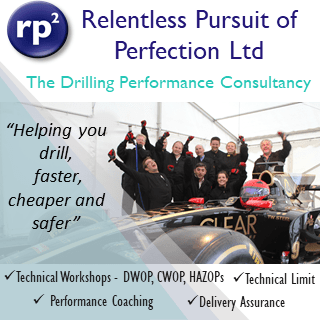