While drilling gas levels - what are your limits, how are they managed?
29 March 2019 Seeking learning / experiences of how teams get ready to plan design, engineer, and prepare for the physical surface effects of drilling porous permeable GAS reservoirs at high ROP. e.g. 8 1/2" wellbores 20-25% porosity, ROP's > 100ft (30m/hr)What do you expect to see via the mud loggers gas detectors,
What are viewed as safe operable limits, best practices to be applied?
What corrective actions are then needed?
What illustrative well DDR's can be provided to support if best or improper practices then resulted?
How much of this is covered in current well control examinations, simulations?
FAIL (Failure Always Invites learning) events in this respect?
regards,
2 Answer(s)
PLEASE LOGIN OR SIGN UP TO JOIN THE DISCUSSION
Support Spread
We need the support of our members to keep our forum online. If you find the information on spread useful please consider a donation

Posted by
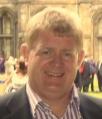
Peter Aird
Drilling Specialist/Well Engineer/Training Consultant
Discussions: 115
Replies: 449
Related Discussions
Drilling Readiness Review - Checklist
Blasting in proximity of existing wells.
Standards and guidelines for well constrution and operations
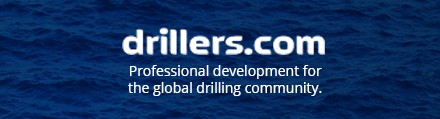
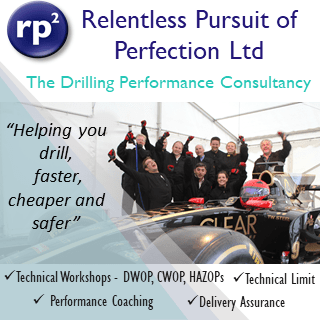