Topic drive string swivel and free rotation capabilities (torque and drag?)
25 June 2019 For those that remember.Kelly gets racked back in its mousehole.
We unlock the blocks to let the string, links and elevators below swivel component now rotate freely when POH/RIH. When into cased hole we then generally locked the swivel component.
Extent of hole condition now represented via drag up/down on the weight indicator and the string visibly seen to rotate anti-clockwise as we POH to see the extent of hole spiralling etc.
We never backreamed as we could not. Majority of wells we simply managed to get out of hole simply by pulling, working string up/down and when excessive drag was noted pumping out in singles etc. Personally never experienced a string left in the ground while drilling tripping with a Kelly rig. (Checking the hole every 30ft drilled to make a connection may with zero upward rotation, have been more beneficial than today realised.)
As we run in the hole again downward drag and string is seen to rotate clockwise. Often when conditions permitted us to do so, we would trip at 1mins / stand (5500ft/hr). RIH one would see the swivel links elevators and string rotate a lot of revs in a hole that was heavily spiral due to bit/bha defects despite practices used. e.g. low rotation / high ROP, poorly designed and optimised bit/BHA stabilisation placement etc often results in a more spiral hole.
Never having really though too much about this before until today ie differences when using a top drive. Is there any raises the following question.
Using a SWOT analysis w.r.t Top drive utilisation.
What are Top drives and string pros/cons and ability to freely rotate the string pros and cons when RIH/POH?
Strengths?
Weaknesses ?
Opportunities?
Threat?
Thoughts, experiences, evident case studies?
Regards,
5 Answer(s)
PLEASE LOGIN OR SIGN UP TO JOIN THE DISCUSSION
Support Spread
We need the support of our members to keep our forum online. If you find the information on spread useful please consider a donation

Posted by
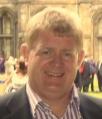
Peter Aird
Drilling Specialist/Well Engineer/Training Consultant
Discussions: 115
Replies: 449
Related Discussions
Avoiding Stick Slip
Jars
Jars Jars Jars
BHA Inspection Criteria
XT 57, Tight Drillpipe Connections
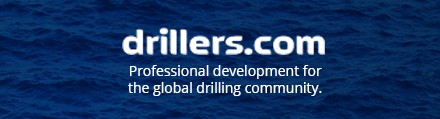
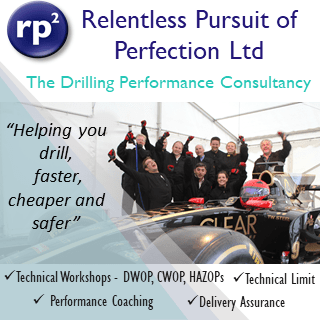