T&D Analysis - Buckling
05 July 2019 Opinion Needed:Performed T&D on an S shaped well on Well Plan on an 8-3/8" BHA, where buckling limit is predicted near the depth the well starts to become vertical. [ Max inclination ~ 15 deg]. Weight to buckle the string helically ~ 5 T in the analysis, on which drilling is operationally not feasible. To double check the results, SLB & HLB were asked to perform the analysis, where SLB results showed the onset of helical buckling at 15 T [ significantly higher value], but HLB results were same as our's [maybe because they use the same software i.e. Well plan] Is it because of different algorithms used for buckling in both the software? What might be the reasons?
Inclination profile and analysis results are attached
P.S All three analysis used the Stiff String model and same friction factors
Documents uploaded by user:
9 Answer(s)
PLEASE LOGIN OR SIGN UP TO JOIN THE DISCUSSION
Support Spread
We need the support of our members to keep our forum online. If you find the information on spread useful please consider a donation

Posted by

Umair Ahmed Baig
Senior Drilling Engineer
Discussions: 17
Replies: 23
Related Discussions
Drilling Rig Computer Hardware
Mathcad users group?
Daily Drilling reporting software
Survey tool error model for Totco inc surveys
Any experience with Drillingsoftware.com casing design software?
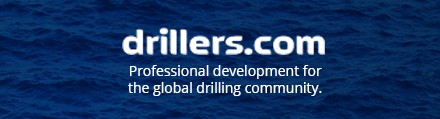
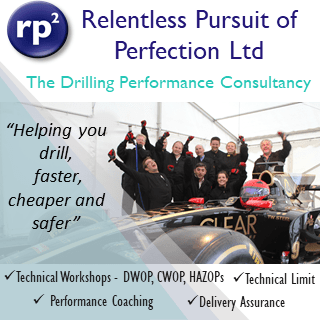