Drill Collar Shoulder Problem
05 September 2019 HiWe are drilling a well and issuing damages on shoulders of drill collars and bit sub at all trips. Damages have been observed on shoulders and only on drill collars not hwdp, dp etc. We have not yet encountered this problem so far.
We have controlled the tool joint compound, it is what we always use.
Connection cleaning has been also checked.
Tong line gauge has been checked again and again and calibrated.
We have high vibration during drilling and stabilizers mostly pulled out highly under gauge.
What is the reason and how can we solve it?
Thanks
9 Answer(s)
PLEASE LOGIN OR SIGN UP TO JOIN THE DISCUSSION
Support Spread
We need the support of our members to keep our forum online. If you find the information on spread useful please consider a donation

Posted by

Adem Buyukdacik
Drilling Manager
Discussions: 1
Replies: 0
Related Discussions
Drilling and completion
TH Drilling Gumbo Issues
Drilling Through a Fault
Wellbore Ballooning
Abnormal Torque with increasing RPM upto 150
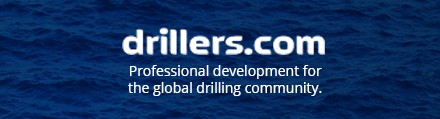
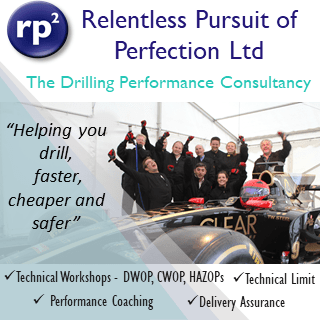