Drilling Through a Fault
19 November 2019We will be drilling a horizontal well and the landing section passes through a fault. Due to the experience on a previous campaign in the field, we plan to drill the 12 ¼” landing section in 2 runs.
The first run to terminate 150ft above the expected fault will be a RSS (point-the-bit) with PDC bit. This will be changed to a dumb iron packed assembly with a PBL sub included to allow the flexibility of pumping different kinds of LCM pills to manage losses.
We will then drill circa 300 ft (3 stands) blind. The section planned for blind drilling is a tangent with inclination of 78.5 deg, azimuth 101 deg and DLS 2.5. The dumb iron assembly will be POOH to revert back to the RSS and drilling continued to the 12 ¼” landing depth /section TD.
The fault is 470ft from the heel of the well and the risk / potential for the packed BHA to drop or build inclination and change azimuth in the 270ft tangent is high. If this occurs, it will cause significantly high DLS to catch-up original trajectory and could adversely impact hole usability (casing running, completion, e.t.c.).
Questions::
1] Does anyone have experience(s) drilling through fault they can share with me, what kind of drilling parameters did you employ if you ran a dumb iron BHA?
2] Any advice on the best way to manage BHA / Formation tendencies / bit walk with the dumb iron assembly with Mill Tooth Bit since the first BHA is RSS with PDC bit to minimize DLS
3] Any rules of thumb for modelling or predicting the dumb iron BHA tendency?
4]The formation is deltaic continuous depositional, and permeability is high. We are drilling with SOBM and have tried every known LCM in the past including cement with minimal success. Does anyone know of any other novel LCM / Total Loss Circulation management strategy?
9 Answer(s)
PLEASE LOGIN OR SIGN UP TO JOIN THE DISCUSSION
Support Spread
We need the support of our members to keep our forum online. If you find the information on spread useful please consider a donation

Posted by

Tayo Ajimoko
PM
Discussions: 2
Replies: 0
Related Discussions
Drilling and completion
TH Drilling Gumbo Issues
Drill Collar Shoulder Problem
Wellbore Ballooning
Abnormal Torque with increasing RPM upto 150
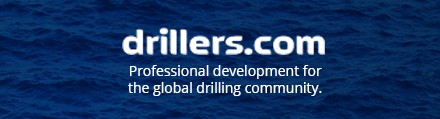
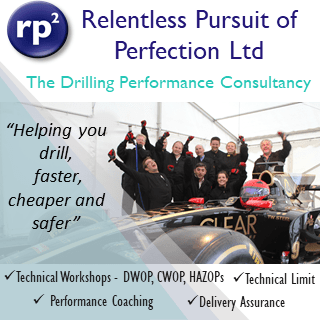