Rigless P&A - wells with CIM/DPG
07 September 2019Hi!
I would like to start a discussion to get some thoughts/opinions from the group on performing a rigless P&A on a well with a chemical injection mandrel and/or downhole pressure gauge located close to the production packer.
There's proven cost reduction in a majority of cases using a rigless approach to well P&A which utilizes the production tubing as a workstring to convey cement plugs. This approach also leaves much of the tubing as possible in the well.
As chemical injection mandrels and smart completions have become more prevalent, it introduces a big complication to the rigless P&A approach - having cables or tubing traverse a cement plug. Regulations do not allow this for a permanent barrier.
How do you perform a rigless P&A on a well with a CIM/DPG close to the packer?
My current thoughts (assuming CIM/DPG is within 100' of packer):
- Isolate the perforated/production interval (squeeze cement or CIBP w/ cement)
- Attempt to pump polymer plugging media down CIM tubing
- Set a ~300' balanced cement plug in tubing and casing as close to the packer as possible. This plug would be across the CIM tubing/DPG cabling and would serve as a TEMPORARY barrier once satisfactory tests are achieved.
- Cut the tubing from ~100' below the depth of the location for the next cement plug.
- N'/D the tree and pull the tubing
- Set CIBP at depth of next plug to serve as PERMANENT barrier
- Run a 1-1/4" workstring to CIBP and spot cement plug.
- Set additional plugs as necessary...
The concern is whether or not the first balanced plug w/ tubing would qualify as a temporary barrier to allow the tubing to be pulled without having to rig up BOPE.
Does anyone have firsthand experience with a similar situation?
Is there any other methodology that would be preferable?
Has anyone used any new technology that is able to defeat the CIM tubing or DPG cabling to allow thru-tubing cement plugs to be set?
2 Answer(s)
PLEASE LOGIN OR SIGN UP TO JOIN THE DISCUSSION
Support Spread
We need the support of our members to keep our forum online. If you find the information on spread useful please consider a donation

Posted by

Dirk Heseman
Project Manager
Discussions: 5
Replies: 7
Related Discussions
Relying on shales as annulus barriers
Cement Plugs in CaBr enviromental
Pump and Pull techniques, high angle wellbores.
Well Abandonment - Control Lines
abandonment work
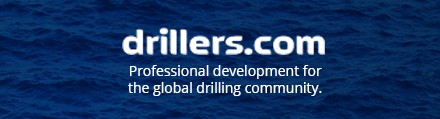
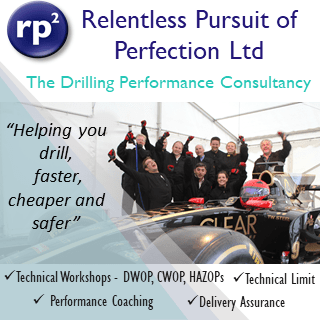