Well Construction & Decommissioning: Tapered Casing strings run as liners
23 February 2021 Dear colleaguesI am throwing out a request to gain knowledge and support to my internal and external networks.
We are engaged in and abandonment and decommissioning campaign in the Caspian Sea.
The wells were drilled in the former Soviet Union times by the Russians. The well were drilled in the 70’s and there are a number of interesting challenges to overcome. Not least in understanding how these wells were designed and constructed.
From the translation of old drilling reports, they were running tapered casing strings 10-¾” x 9-⅝” . Running the deeper 9-⅝” sections on drill pipe and then cementing in place; the upper 10-¾” sections were then run, cemented and then connected somehow to the lower section.
If anybody has experience of this and can help me understand the connection process whether it would be overshot, stabbed in or even rotated to form the connections.
If anybody can educate me on this it would be greatly appreciated.
Many thanks
John
6 Answer(s)
PLEASE LOGIN OR SIGN UP TO JOIN THE DISCUSSION
Support Spread
We need the support of our members to keep our forum online. If you find the information on spread useful please consider a donation

Posted by
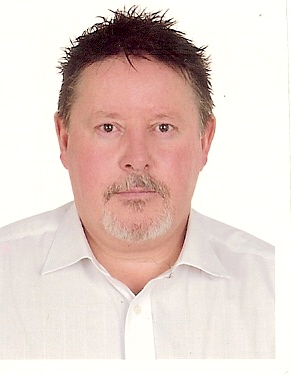
John Moffatt
Senior A&D Engineer
Discussions: 1
Replies: 1
Related Discussions
Relying on shales as annulus barriers
Cement Plugs in CaBr enviromental
Pump and Pull techniques, high angle wellbores.
Well Abandonment - Control Lines
abandonment work
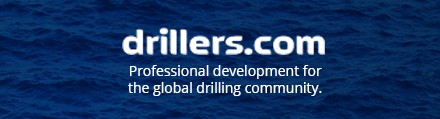
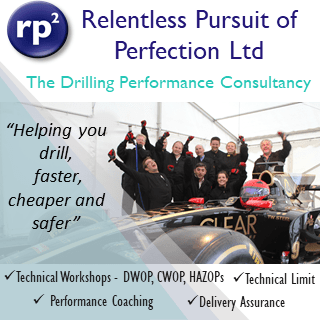