Conductor wobble in soft soils - CAN solutions?
27 September 2016East coast of India has some extreme rapid depositional systems that deposits very soft clay bound soils into the deep and ultra deepwater environments. In other regions similar depositional systems likely exist. i.e. very soft seabeds.
e.g. In shallow water, jack ups and semis also often experience problems in this first drilling phase, float boxes and other contraptions often needed as a foundation pipe to be able to get cuttings and cement back to surface.
When these areas move into development wells. The stand alone conventional wells in my view will not be enough. Because what we have observed is that conductor movement will create circumferential hole around the conductor and 'conductor wobble' results (although one never sees the conductor move because cyclic movement is so slow). However this gap surely presents a long term problem and potential risk e.g. < fatigue life of conductor pipe.
Thinking suggests that the solution is akin to what we do for suction anchors, support for templates etc. I.e. Self penetrate and pump in a 'Conductor anchor node 'CAN' for short.
These are typically 10-15m in length and up to 6m in diameter. They self penetrate and a simply ROV hydraulic pump sucks out the water from within the CAN and foundation pipe is sucked into the seabed to deliver a secure foundation axial and bending resistant system for the life of the well.
So why are drillers not using more of these? Where recently offshore Norway and spreading into UK, CAN's are starting to be used/applied.
One for the geotechnical people to share views and thoughts please.
3 Answer(s)
PLEASE LOGIN OR SIGN UP TO JOIN THE DISCUSSION
Support Spread
We need the support of our members to keep our forum online. If you find the information on spread useful please consider a donation

Posted by
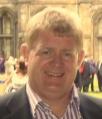
Peter Aird
Drilling Specialist/Well Engineer/Training Consultant
Discussions: 115
Replies: 449
Related Discussions
Mud mats in deepwater.
Recent trends in "Jetting, driving, drilling in conductors in deepwater?".
Soil shear strength, fracture gradient in shallow deepwater sediments?
Mud volcano's
Deepwater Ooze?
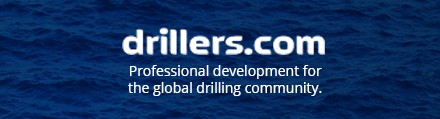
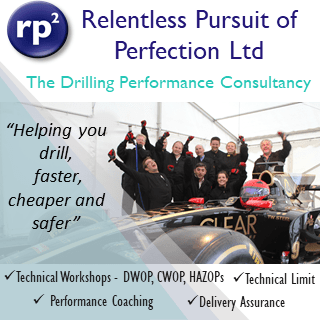