Mud mats in deepwater.
20 October 2009 To aid the process of updating current deepwater 'best practise guidelines' the issue of mud mats is another interesting thread as illustrated by industry 'drillers club' comments collated so far.Any other practices of note in this area thus appreciated.
Peter.
10 Answer(s)
PLEASE LOGIN OR SIGN UP TO JOIN THE DISCUSSION
Support Spread
We need the support of our members to keep our forum online. If you find the information on spread useful please consider a donation

Posted by
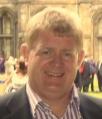
Peter Aird
Drilling Specialist/Well Engineer/Training Consultant
Discussions: 115
Replies: 449
Related Discussions
Recent trends in "Jetting, driving, drilling in conductors in deepwater?".
Soil shear strength, fracture gradient in shallow deepwater sediments?
Mud volcano's
Deepwater Ooze?
Mid Way Riser Slope Indicator
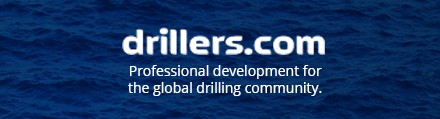
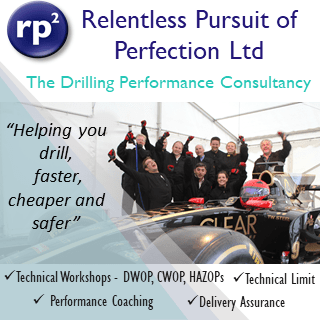